Optimizing Manufacturing Processes
SoP, CIL, OPL, and Centerline Development
Standard Operating Procedures
We work alongside your existing team members and support network to develop simple, efficient guides covering the orientation, operation, changeover, quality, shutdown, cleaning, and troubleshooting of your machine centers.
CIL: Clean, Inspect, Lubricate
Working with your maintenance, quality, operation, and supervisory staff, as well as your equipment manufacturers, we develop CIL standards to ensure the longevity and efficient operation of your machine centers.
Centerlines
Time Studies & Downtime Analysis
Through analysis of your existing operations and feedback from operators we assist in identifying critical adjustment points. Determining the appropriate basic conditions and developing a centerline audit will ensure your equipment can function at peak efficiency.
Through rigorous analysis of daily operations, we can identify your top causes of downtime and eliminate the root causes of downtime events.
All the Tools You Need to Succeed
The standard operating procedures and learning guides created by our engineers are easily handed off to your team. The guides are a living document that will facilitate the training of new subject matter experts on existing and future equipment.
Our insights to your unique processes allow the creation of learning materials that can be utilized in onboarding new team members and creating checklists to ensure consistent success in the operation, shutdown, cleaning, and changeover of your machine centers.
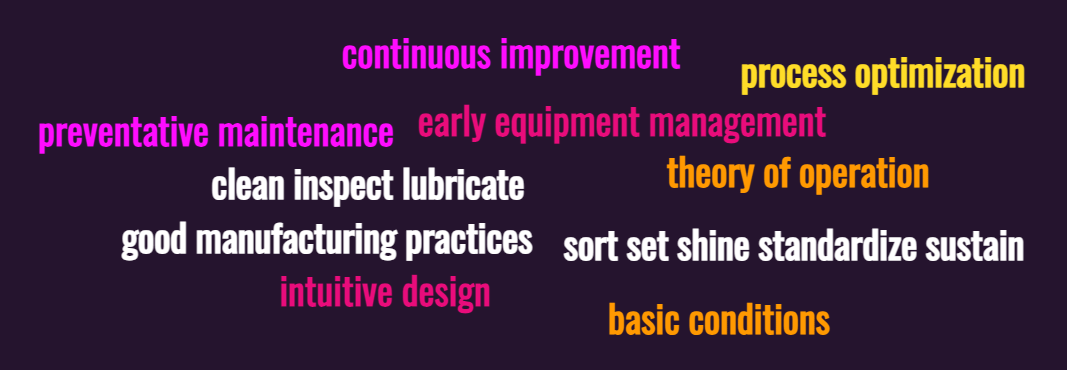
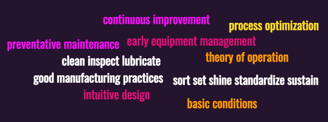
Startup
Improve the ease of operation and maintenance through Early Equipment Management; work with the customer to impact the final design and function of the production line
Document knowledge from equipment manufacturers during installs to create standard operating procedures
Facilitate communication between the operators and technicians to optimize the functionality of machine centers
Document centerlines and establish matchmarks to optimize changeovers and ensure alignment to basic conditions
Perform time studies on equipment and eliminate sources of downtime
Train operators on new machine centers using the orientation, safety, operation, changeover, shutdown, and cleaning documents created
Ensure the equipment meets the requirements of site acceptance tests
Daily Operations
Create standard operating procedures that optimize daily tasks
Utilize checklists to ensure correct order of operations and facilitate startup, operation, changeover, and shutdown procedures
Train operators on the theory of operation to increase throughput
Conduct time studies on machine centers to identify and eliminate sources of downtime
Establish preventative maintenance practices to minimize unplanned downtime events
Audit lines to ensure efficient access to wear parts, raw materials, and cleaning supplies
Utilize planned downtime events to audit machine centers and perform cleaning, inspection, and lubrication tasks
Identify wear parts and failure points to prepare troubleshooting guides
Training
Work with existing subject matter experts to create standard operating procedures that optimize line performance
Train operators through use of created materials
"Train the trainer" to ensure the creation of future subject matter experts